客戶簡介
公司位於台中,擁有最優質產業供應--廠內一條龍生產。客戶從詢問/討論/報價/下單 準時交貨,能配合著客戶的訂單及需求,做高效服務的整合及提供意見。主要出口市場是歐美等地。
遇到的問題
1.因為都須透過人員KEY IN ERP但有時候太忙所以忘記KEY IN導致無法銷貨,流程上常常會造成都在快下班才將單據補齊結案,無法即時得知生產進度與物料庫存量。
2.ERP途程單人工管理,現場設備種類多,數據回報都需要人員回報,數據準確性與回報的時間都會差距一天以上,無法立即得知生產進度也難以計算生產效益。
3.太多老師傅的經驗希望可以透過系統標準化,透過數據回饋讓目前的流程與數據更加真實,讓經驗與流程標準化進行,來解決目前人力缺乏的問題。
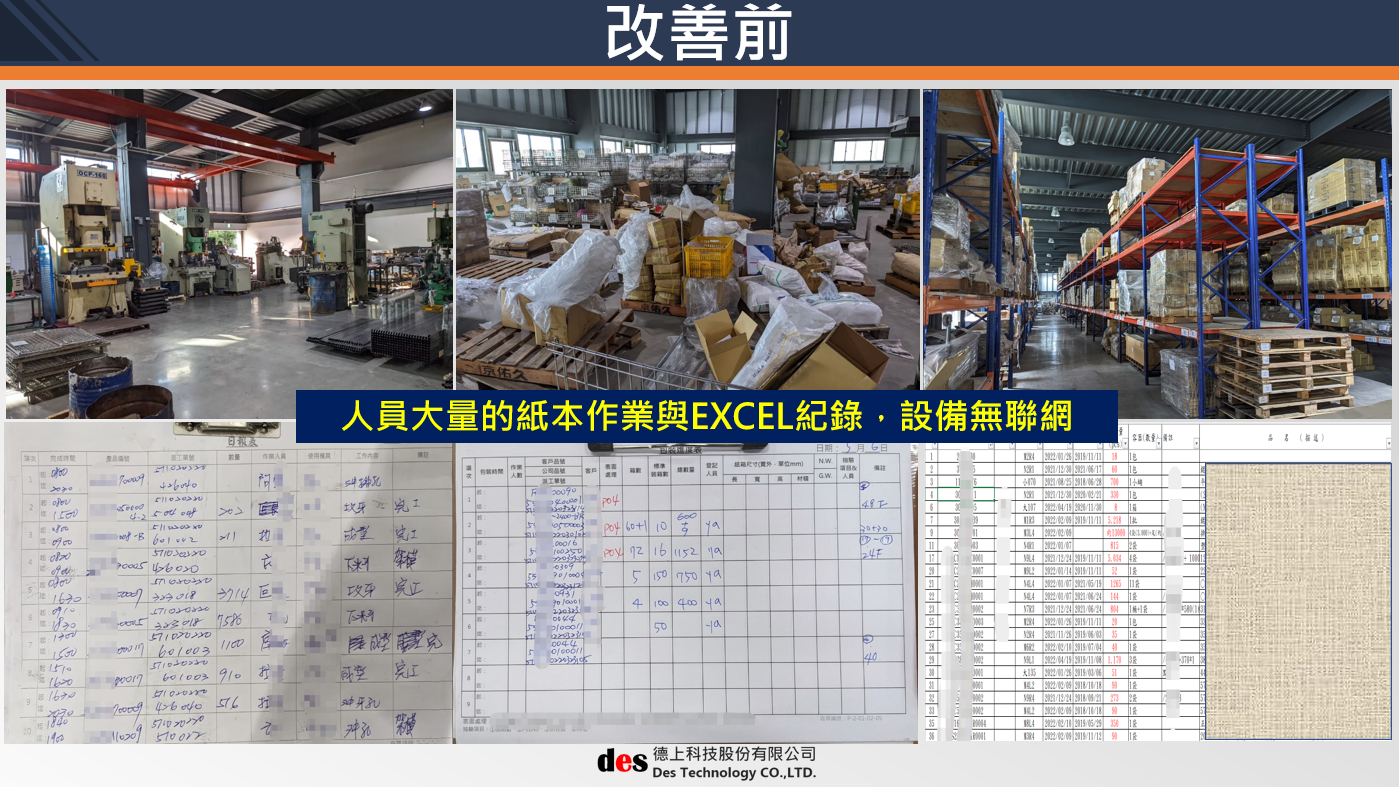
現場包含加工、焊接、包裝,一條龍的製程,因為都是客製品,物料也分散至各樓層庫存與呆滯品控管困難
現場流程梳理改善顧問服務,找出現場加工至物料控管流程中慣性的魔鬼
ERP&IOT異質整合
導入VIS報工系統、WMS倉儲管理系統、可視化生產看板、物料看板
全廠產品條碼化,目的是要讓認識產品不在需要花費大量的時間只需要會操作行動裝置即可作業,從收料開始到出貨WMS系統管理,讓物料在哪裡與為什麼要出庫的都清楚記錄,一步一步改善物料的問題。
協助客戶與ERP廠商共同討論異質整合的方式與需求,從製程的調整到報工進出站、物料的領與入所回饋的資訊將都是自動產生單據,大幅度的降低人員KEY的時間
建立IOT回饋並整合報工系統讓生產數據能夠即時回饋,讓數據可性度大幅提升。
.png)
輔導後帶來哪些效益
公司位於台中,擁有最優質產業供應--廠內一條龍生產。客戶從詢問/討論/報價/下單 準時交貨,能配合著客戶的訂單及需求,做高效服務的整合及提供意見。主要出口市場是歐美等地。
遇到的問題
1.因為都須透過人員KEY IN ERP但有時候太忙所以忘記KEY IN導致無法銷貨,流程上常常會造成都在快下班才將單據補齊結案,無法即時得知生產進度與物料庫存量。
2.ERP途程單人工管理,現場設備種類多,數據回報都需要人員回報,數據準確性與回報的時間都會差距一天以上,無法立即得知生產進度也難以計算生產效益。
3.太多老師傅的經驗希望可以透過系統標準化,透過數據回饋讓目前的流程與數據更加真實,讓經驗與流程標準化進行,來解決目前人力缺乏的問題。
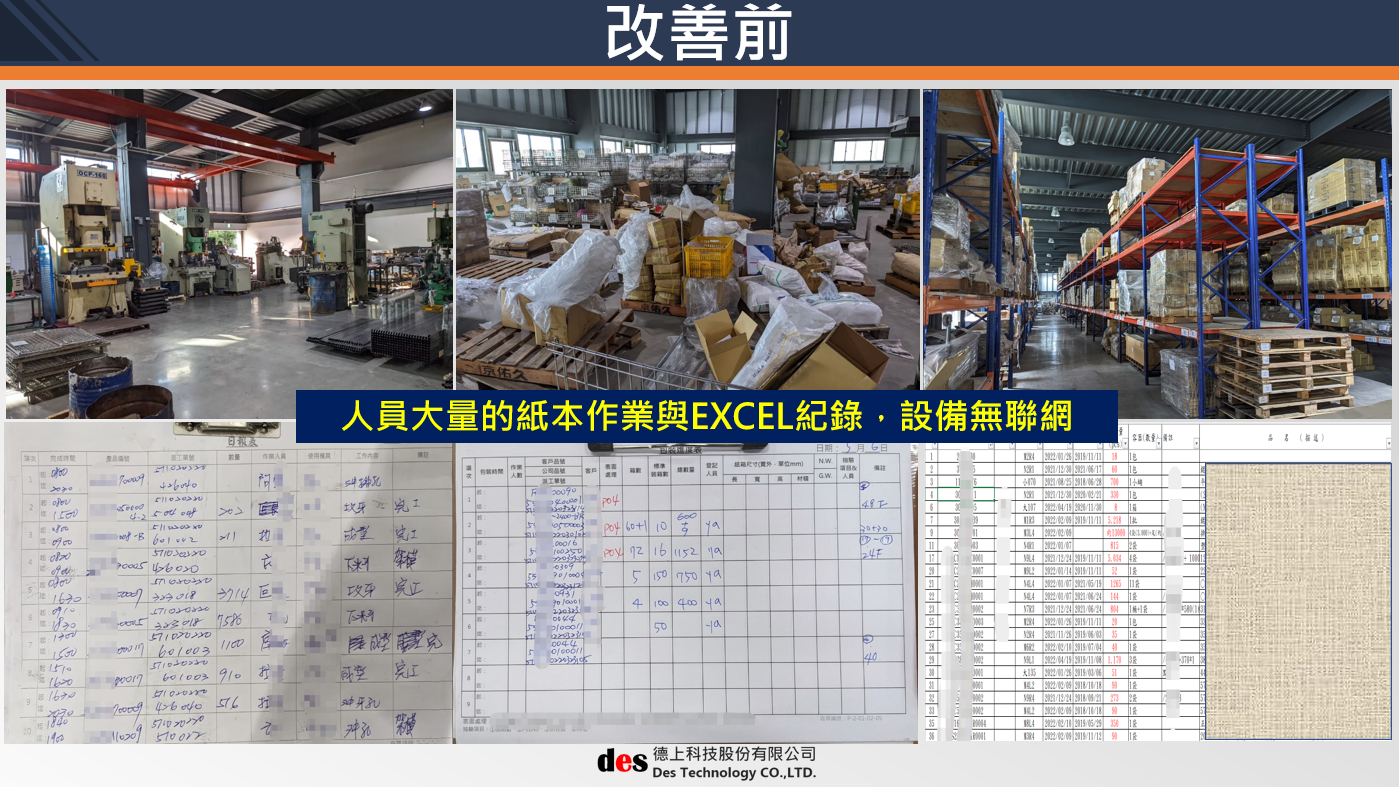
現場包含加工、焊接、包裝,一條龍的製程,因為都是客製品,物料也分散至各樓層庫存與呆滯品控管困難
顧問輔導內容
現場流程梳理改善顧問服務,找出現場加工至物料控管流程中慣性的魔鬼
ERP&IOT異質整合
導入VIS報工系統、WMS倉儲管理系統、可視化生產看板、物料看板
全廠產品條碼化,目的是要讓認識產品不在需要花費大量的時間只需要會操作行動裝置即可作業,從收料開始到出貨WMS系統管理,讓物料在哪裡與為什麼要出庫的都清楚記錄,一步一步改善物料的問題。
協助客戶與ERP廠商共同討論異質整合的方式與需求,從製程的調整到報工進出站、物料的領與入所回饋的資訊將都是自動產生單據,大幅度的降低人員KEY的時間
建立IOT回饋並整合報工系統讓生產數據能夠即時回饋,讓數據可性度大幅提升。
.png)
輔導後帶來哪些效益
◆減少紙本作業時間:60分鐘/人(人工作業)→3分鐘
◆減少生產拿錯應配發物料的頻率:5次/月→1次/月。
◆縮短處理生產資訊時間:50分鐘/天→1秒。
◆生產進度透明化,故目前提升產能5%效益。
◆降低找料與備料所浪費的時間:30分鐘/天→10秒。
智慧製造的前進真的需要由上至下的認同與改變,也感謝此案廠的老闆與管理部門支持,大家才能往同一個目標前進,固然過程真的蠻波折的,從製程到倉儲的模式改變
每一個流程都會有不同的驚喜,需要一關一關的突破,當然目前還在持續優化中,讓智慧製造能夠完整的落地實證,讓標準數位化能夠寫入企業的DNA中。
◆生產進度透明化,故目前提升產能5%效益。
◆降低找料與備料所浪費的時間:30分鐘/天→10秒。
智慧製造的前進真的需要由上至下的認同與改變,也感謝此案廠的老闆與管理部門支持,大家才能往同一個目標前進,固然過程真的蠻波折的,從製程到倉儲的模式改變
每一個流程都會有不同的驚喜,需要一關一關的突破,當然目前還在持續優化中,讓智慧製造能夠完整的落地實證,讓標準數位化能夠寫入企業的DNA中。
寬立顧問團隊歡迎您來詢問
我們將提供專業的服務,與您一同邁向智慧製造